There are many different types of fabric printing methods, and they all yield different results. The type of textile printing used is often based on a number of considerations, from print runs, to durability. We have pulled together some of the most popular, or most commonly used methods, and explained them below.
Fabric Printing Methods
1. Stamp Printing
This method is pretty self-explanatory. A stamp is created, which is then used to imprint onto the fabric. Similar to the ink pad stamps you used growing up, your design is cut into the stamp, which is then dipped into the ink. Using even pressure, you transfer your design from the stamp onto the textile. Although we’ve come a long way from ink stamps, the level of detail that you can get from stamp printing is limited, so this is not suitable for the more intricate designs.
Pros
- No need for machines
- Design is always exact
- Great for small runs
- Cost-effective
Cons
- Not very detailed
- Can’t make large quantities
- Only one design per stamp
- Quality is inconsistent

2. Transfer Printing
Another method is using transfer paper. This is a special paper for purchase at supermarkets or craft shops. You can use a standard household printer to print your design onto the transfer paper, which can then be printed onto your chosen fabric with a standard, household steam iron. Transfer printing can be upscaled and done professionally on larger runs; however, it will leave a shiny film or surface texture on your fabric. Transfer printing is not a permanent method of fabric printing, for it can crack and peel with multiple washes, and often fades.
Pros
- Can print with standard printer
- No specialist equipment needed
- Great for small runs
- Easy to print and transfer
Cons
- Leaves a surface texture/film
- Transfers are single-use
- Peels, cracks, and fades
- Can suffer from low resolutions
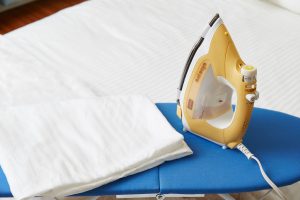
3. Screen Printing
As we move towards the other end of the printing scale, we start to see methods that are used more commonly within the professional world of textile printing. Silkscreen printing is most common within the business industry. This method of printing uses a stencil and a nylon mesh to create the print design. Waterproof material will block out the spaces that you want your design to appear on, and then those blocked out spaces are flooded with ink. Due to the way that this method is carried out, you can only use one color for each screen; however, it does produce fantastic replications.
Pros
- Amazing image reproductions
- Long-lasting
- Ideal for sharp edges and solid blocks of color
- Cost-effective for large runs
Cons
- One color per screen – not ideal for multi-colored designs
- Very labor-intensive, impractical for small runs
- Not great for photos/color gradient
- Creates a lot of waste

4. Dye Sublimation
This is a multi-step process that produces some of the best results of all the fabric printing methods. Designs are printed onto a thermal transfer paper, known as dye sublimation paper. The paper is used to print the design onto the fabric. Both heat and pressure are used to permanently bond the inks to the fibers of the fabric, leaving your fabric as soft as it was before it was printed on. The deep infusion technique penetrates special water-based inks deep into the textile, making your print permanent. Perfect for intricate details as well as colors.
Pros
- Amazing image reproduction that is permanent
- Leaves no texture or residue on the fabric
- Eco-friendly, water-based inks don’t fade or peel
- Suitable for all size print runs
Cons
- Not for use on natural fabrics, only on poly textiles
- Requires specialist equipment and dyes
- More expensive printing method
- Requires in-depth knowledge and experience
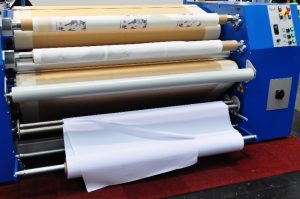
5. Pigment Printing
Pigment printing is one of the most popular printing techniques for use on cellulose fibers, making them ideal for use on natural fabrics. This fabric printing method can also work on synthetic materials, making it versatile. It is a localized technique which involves applying dyes to the area of fabric that you want your design to be located. The process is repeated to make the color appear stronger on the fabric.
Pros
- Bright printing with permanent color
- Easy to do, good color matching
- Cost-effective, no high-end machinery
- High-speed printing technique
Cons
- Not applied directly to the fabric
- Uses binders which leave a coating on the textile
- Color lessens when repeatedly used over the same material
- Dye sits on top of the fibers rather than embeds

6. Reactive Printing
Reactive printing is one of the heat-activated fabric printing methods. It is done by pre-coating the fabrics with a binder (similar to that of pigment printing) and a printing additive. It prints a dye or wax onto the fabric, and the heat reaction permanently bonds the image to the textile. Put simply, it is similar to coating the fabric with the design, then steaming the fabric to create a reaction which bonds the design to the material.
Pros
- Creates a chemical bond between the ink and fabric fibers
- Works well on natural textiles
- Wash-fast and rub-fast
- Outstanding color vibrancy
Cons
- Requires pre-treatment
- Also requires post-treatment
- Not particularly easy to carry out
- Not the most cost-effective printing method
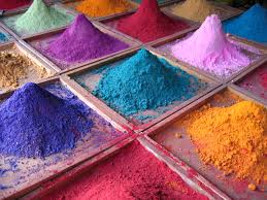
Try your own fabric printing online – it’s so much easier than you think.
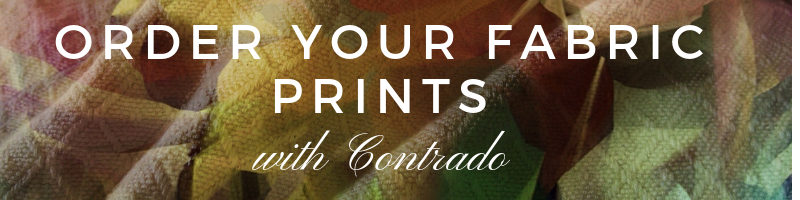

Hi I’m looking to have an image printed on fabric. Don’t know anything about this. I’m looking to design some clothes. Don’t know the best fabric to use for this adventure.
George
Hi George, thanks for reaching out! We’d be happy to help. Printing an image on fabric is quick and simple. Just head to https://www.contrado.com/all-fabrics and find your perfect fabric to print an image on! Once you press ‘Start Design’, you’ll be taken to our design interface where you can easy upload your image and position it how you’d like. Make sure to select the correct dimensions. Alternatively, if you just want to order clothes without making them, you can browse our extensive range of clothing here: https://www.contrado.com/clothing 🙂 I hope that helps! Do let me know if you have any more questions!
Hi I’m trying to get information re: printing on textiles
Hi! I have a logo that i would like to put on clothing, also scrub hats. I dont know anything about printing logos..